PRESSURE & TEMPERATURE RATINGS
Working Pressure | 16bar |
Shell Testing Pressure (x1.5) | 24bar |
Seat Testing Pressure (x1.1) | 17.6bar |
Working Temperature | -20°C … 110°C (EPDM) -10°C … 80°C (NBR) |
Suitable Media | Water, Oil & Gas |
Material Specification
Body | Ductile Iron |
Disc | Ductile Iron Aluminium Bronze Stainless Steel 304 Stainless Steel 316 |
Shaft | Stainless Steel 410 Stainless Steel 431 |
Seat Ring | EPDM / NBR |
O-Ring | EPDM / NBR |
Bushing | Bronze |
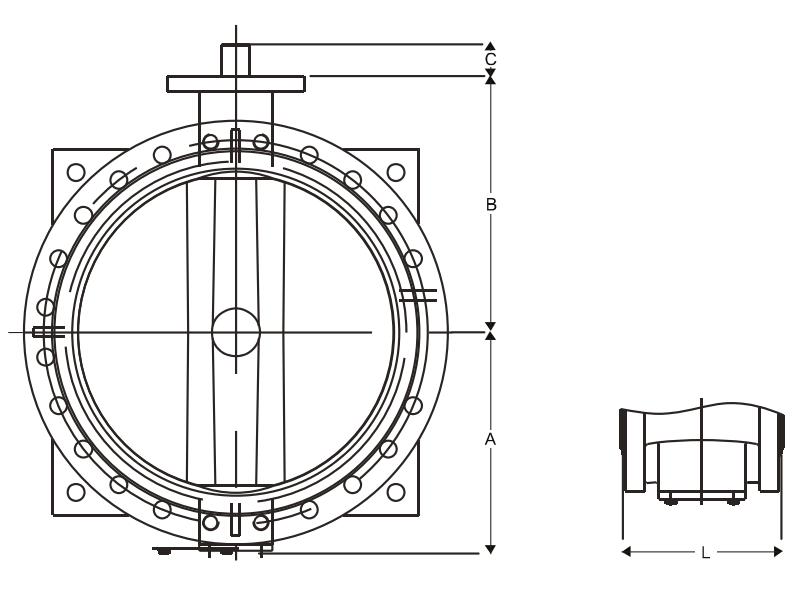
DIMENSIONS
DN | (mm)
(inch) |
50
2 |
65
21/2 |
80
3 |
100
4 |
125
5 |
150
6 |
200
8 |
250
10 |
300
12 |
350
14 |
400
16 |
450
18 |
500
20 |
600 24 |
A | 82.5 | 92.5 | 100 | 110 | 125 | 142.5 | 170 | 202.5 | 230 | 260 | 290 | 320 | 357.5 | 430 | |
B | 127.5 | 136 | 146 | 156 | 176 | 186.5 | 226 | 274 | 304 | 330 | 340 | 400 | 500 | 535 | |
C | 56 | 56 | 56 | 56 | 56 | 56 | 70 | 70 | 76 | 76 | 107 | 107 | 107 | 135 | |
L | 108 | 112 | 114 | 127 | 140 | 140 | 152 | 165 | 178 | 190 | 216 | 222 | 229 | 267 |
DN | (mm)
(inch) |
700
28 |
800
32 |
900
36 |
1000
40 |
1200
48 |
1300
52 |
1350
54 |
1400
56 |
1500
60 |
1600
64 |
1800
72 |
2000
80 |
2200
88 |
2400 96 |
A | 507 | 573 | 634 | 693 | 789 | 968 | 1066 | 1055 | 1025 | 1041 | 1164 | 1350 | 1430 | 1610 | |
B | 560 | 620 | 620 | 735 | 917 | 990 | 1046 | 1000 | 1060 | 1150 | 1200 | 1360 | 1500 | 1650 | |
C | 130 | 130 | 130 | 150 | 150 | 200 | 200 | 200 | 200 | 200 | 200 | 200 | 300 | 300 | |
L | 292 | 318 | 318 | 410 | 470 | 490 | 490 | 530 | 570 | 600 | 670 | 760 | 800 | 850 |
Cast Iron 1 – Stage Worm Gear and Handwheel
Carbon Steel Gear Box Shaft
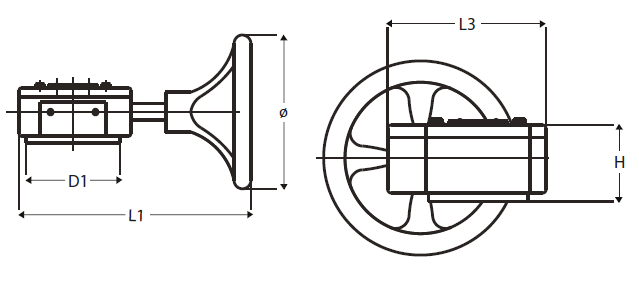
VALVE DIAMETER | D1 | ø | H | L1 | L3 |
DN50 – DN80 | 65 | 150 | 33 | 216 | 127 |
DN100 – DN150 | 90 | 150 | 33 | 216 | 127 |
DN200 – DN250 | 125 | 285 | 36 | 303 | 170 |
DN300 – DN350 | 125 | 285 | 40 | 300 | 190 |
DN400 | 175 | 385 | 79 | 300 | 190 |
DN450 – DN500 | 175 | 390 | 108 | 397/427 | 279 |
Cast Iron 2 – Stage Worm Gear and Handwheel
Carbon Steel Gear Box Shaft
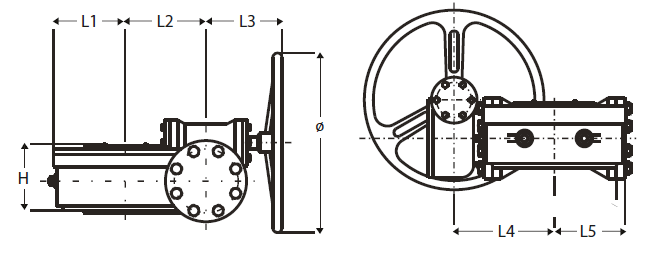
VALVE DIAMETER | ø | H | L1 | L2 | L3 | L4 | L5 |
DN400 – DN500 | 285 | 125 | 107 | 100 | 156 | 168 | 107 |
DN600 | 285 | 125 | 107 | 100 | 156 | 168 | 107 |
DN700 – DN800 | 425 | 149 | 146 | 140 | 197 | 230 | 146 |
DN900 – DN1000 | 425 | 185 | 201 | 196 | 203 | 279 | 201 |
DN1200 | 425 | 216 | 185 | 240 | 203 | 311 | 255 |
DN1300 – DN1400 | 510 | 267 | 208 | 345 | 258 | 435 | 355 |
DN1500 – DN1600 | 510 | 312 | 316 | 410 | 237 | 450 | 425 |
DN1800 | 510 | 326 | 360 | 460 | 237 | 466 | 475 |
DN2000 | 600 | 480 | 410 | 602 | 265 | 725 | 630 |
DN2200 – DN2400 | 600 | 570 | 442 | 696 | 364 | 742 | 726 |
INSTALLATION & OPERATION GUIDE
- Ensure sufficient space for valves for easy installation, operation, maintenance and replacement.
- Verify the valves are suitable for the operating condition such as medium, operating pressure / temperature, etc.
- Check the I.D. of the flange and pipe to ensure free disc movement.
- Valves shall be mounted on flanges only after the counter flanges have been welded to pipe and cooled down to the atmospheric temperature. Welding heat may damage the rubber seat of the valves. Never weld the flanges with valves installed. No gasket is required for installation of rubber seated butterfly valves.
- Position the valves carefully between flanges. Accurate centering between flanges is essential to prevent any damages and problems during operation.
- Valves should be installed by placing bolts through the hole and tightening carefully, ensuring even contact between the flange and seat. Too tight of space may cause damages to the seat and should be avoided.
- Cross tighten all the bolts diagonally to distribute the loads evenly over the valves.
- Turning the valves to ensure sufficient disc clearance.
- Valves equipped with manual operators must be operated manually. Excessive external force on the operation of valve may damage the valve and / or operator.
- Blind flange with short pipe should be used for dead end installation.