TECHNICAL SPECIFICATIONS
Working Pressure | 16bar . |
Shell Testing Pressure | (x1.5) 24bar |
Seat Testing Pressure | (x1.1) 17.6bar |
Working Temperature | -10°C … 120°C |
Suitable Media | Water |
Material Specification
Part | Material | Specification |
Body | Ductile Iron | EN-JS 1050 |
Bonnet | Ductile Iron | EN-JS 1050 |
Stem | Stainless Steel 410(DN65…DN300) Stainless Steel 431(DN350…DN600) |
EN 10088-3 1.4006 EN 10088-3 1.4057 |
Balancing Cone | Ductile Iron | EN-JS 1050 |
Disc | EPDM coated DI | EN-JS 1050 |
Gland | Brass (DN65…DN150) Ductile Iron (DN200…DN600) |
EN 12165 CW617N EN-JS 1050 |
Gland Nut | Brass | EN 12165 CW617N |
Orifice Insert | DZR Brass | EN 12165 CW602N |
Measuring Plug | DZR Brass | EN 12165 CW602N |
Handwheel | Ductile Iron | EN-JS 1050 |
Packing | Graphite | Non-Asbestos |
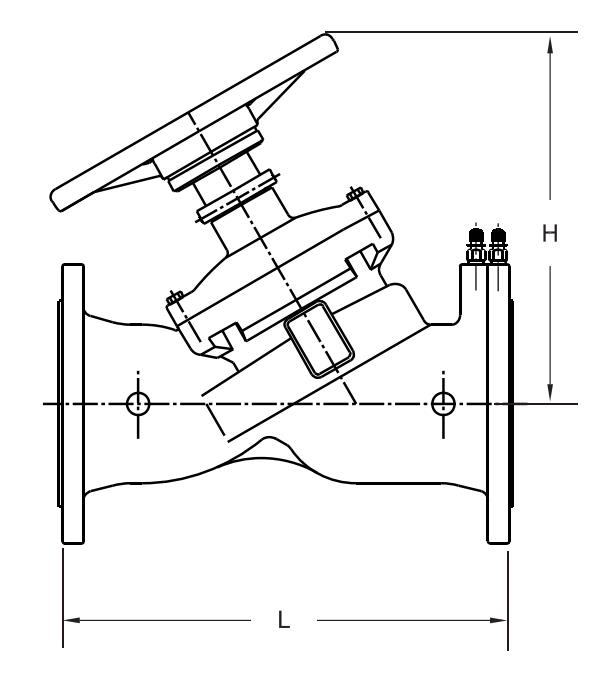
DIMENSIONS
DN | (mm)
(inch) |
65
21/2 |
80
3 |
100
4 |
125
5 |
150
6 |
200
8 |
250
10 |
300
12 |
350
14 |
400
16 |
450
18 |
500
20 |
600
24 |
L | 290 | 310 | 350 | 400 | 480 | 600 | 730 | 850 | 980 | 1100 | 1200 | 1250 | 1450 | |
H | 265 | 270 | 310 | 340 | 340 | 537 | 570 | 690 | 685 | 965 | 1020 | 1065 | 1180 | |
D | 200 | 200 | 240 | 290 | 290 | 350 | 420 | 420 | 420 | 640 | 640 | 640 | 640 | |
Kvs(Fully Open) | 104 | 116 | 213 | 333 | 476 | 768 | 1153 | 1743 | 1798 | 2338 | 2698 | 3708 | 4500 | |
Handwheel Turns | 8 | 8 | 8 | 8 | 8 | 12 | 12 | 18 | 18 | 24 | 24 | 24 | 24 |
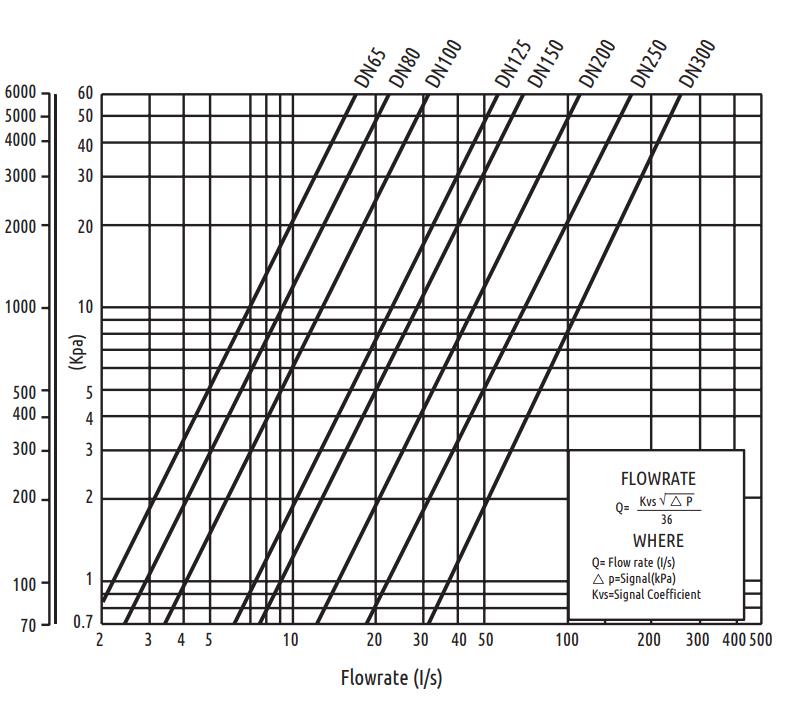
DN | (mm)
(inch) |
65
21/2 |
80
3 |
100
4 |
125
5 |
150
6 |
200
8 |
250
10 |
300
12 |
Kvs | 104.00 | 116.00 | 213.00 | 333.00 | 476.00 | 768.00 | 1153.00 | 1743.00 |
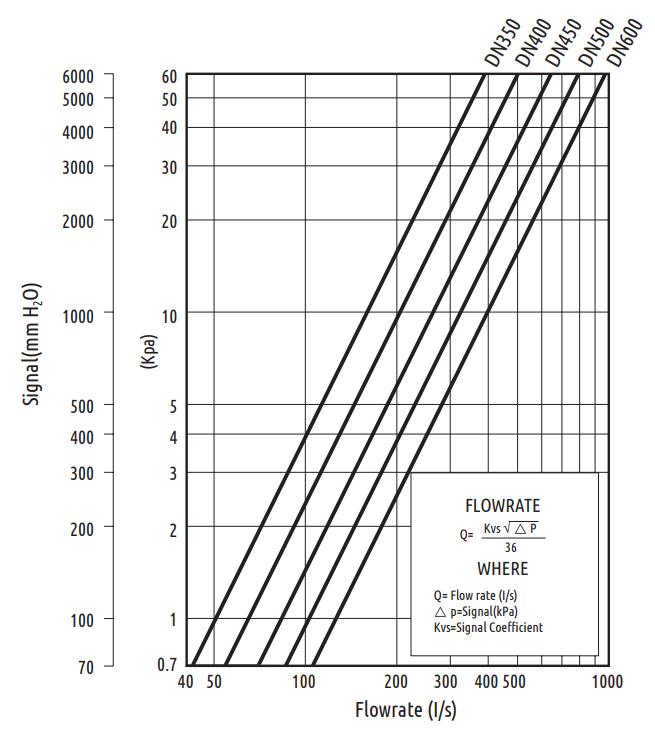
DN | (mm)
(inch) |
350
14 |
400
16 |
450
18 |
500
20 |
600
24 |
Kvs | 1798.00 | 2338.00 | 2698.00 | 3708.00 | 4500.00 |
INSTALLATION & OPERATION GUIDE
Install the Double Regulating Valve in the pipe line by ensuring the arrow marking on the valve is same direction as piping flow.
To achieve flow measurement accuracy, it is essential that the piping on the inlet and outlet of the valve is straight and has a minimum length equivalent to 5 Diameters (5D) inlet and 2 Diameters (2D) outlet as shown. If the valve is install at the discharge side of a pump set, it is essential that the straight pipe length between pump outlet and valve has a minimum length of 10 Diameters (10D).
Gaskets must be used and assembled between valve and flanges. This will ensure the installation is concentric with pipe line and better accuracy is obtained.
Design flow is achieved by pre-setting valve’s opening position, which could be read from scales at the handwheel. Contact your local distributor for information on electronic commissioning meter.
To lock the pre-setting of the valve, push the limitation ring at the scales at the bottom of the handwheel, tighten the screw using the hexagon wrench.
Valve must not be lifted by holding the handwheel.
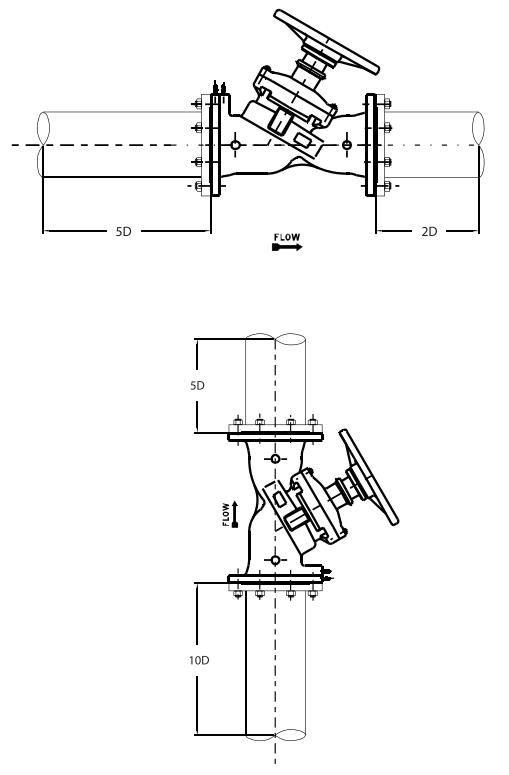